Latest topics
» Tough Life of a Resin Beadby ioncube Fri Jul 19, 2013 8:16 pm
» Final Year Projects Suggestions
by ioncube Fri Jul 19, 2013 2:48 pm
» Tracking Natural Gas Via Flowmeters
by ioncube Sat Sep 08, 2012 11:04 pm
» Maximising Heat-Transfer Fluid Life
by ioncube Thu Aug 23, 2012 6:16 pm
» Exercise your Brain
by ioncube Thu Jul 19, 2012 12:49 pm
Level Measurements - Fingertips Facts
Page 1 of 1
Level Measurements - Fingertips Facts
I am going to summarise various techniques for level measurement illustrated by infographics. Plus the rules of thumb for their respective area of applications:
Effective level measurement helps ensure smooth, continuous processes by maintaining material inventory at economic quantities, and maximizes plant output by preventing spillage, system clogging and process upsets. In chemical process industries (CPI) applications, level measurement of liquids, powders and slurries are often complicated by the presence of steam, dust, foam, turbulence, caking or condensate, as well as high temperatures and pressures.
The diversity of challenging conditions dictates multiple technologies for level measurement, which can be divided into point level measurement and continuous-measurement techniques. Point-level measurement monitors material level at a predetermined point, which could be a high level to avoid spillage, or a low level to avoid running empty. Continuous level measurement monitors materials constantly, noting any fluctuations and changes. Here, brief descriptions of common level--measurement technologies are presented.
pressure differential is the pressure of the liquid column of the tank. Changes in the liquid composition or temperature can create a false reading, but if the fluid density remains constant, this technique provides a true level reading. Differential-pressure devices require sealed fluid in pressurized vessels.

Electromechanical devices (Figure 1) A motor-operated paddle inside a vessel stops rotating when its sensor becomes covered by liquid or solid material. The principle is also applied to vibrating forks that detect material when their vibration speed slows. Paddle sensitivity can be adjusted for varying material properties. The cost-effective and low-maintenance electromechanical designs are well-suited for solids, such as plastic pellets, carbon black, fertilizer, rubber and Styrofoam chips and beads. The paddle switch can handle bulk densities as low as 35 g/L. The technology is completely independent of material dielectric properties.
in the probe’s capacitance when either air or material is present. The measurement system also requires an earth reference to complete any circuit and allow current flow. Capacitance technology is widely used, can handle a range of applications, and produces accurate and repeatable results. Chemical compatibility with the device must be taken into account,
since capacitance is a contact technique. Any changes due to temperature or chemical composition cause the dielectric property of the material to change, resulting in errors and the need to recalibrate. With one opening required in a vessel, capacitance technology is easy to install, and has no moving parts to wear out. Custom probes are available for aggressive chemicals. Calibration of capacitance instruments is best done manually, which can be time-consuming.
between sound burst and return echo is proportional to the distance from the transducer to the material in a vessel. Ultrasonic technology is a preferred option for continuous level measurement. Since ultrasonic instruments measure from
top down, there is virtually no contact with the material. Ultrasonic technology is easy to install and has no moving parts. In addition, it is not affected by changing dielectric properties or vessel shape. However, dust, vapor or foam can affect even the most advanced devices.
So summing up all this:
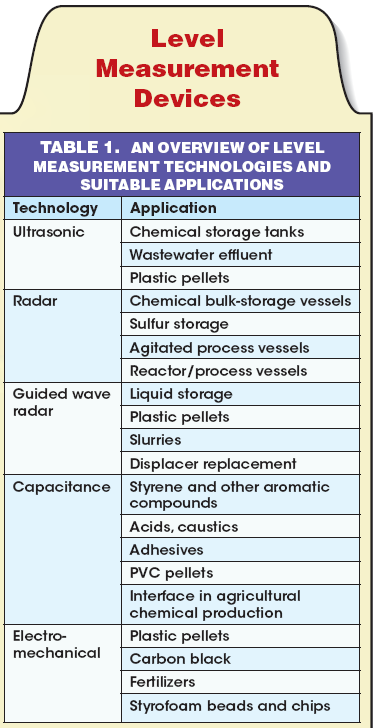
Effective level measurement helps ensure smooth, continuous processes by maintaining material inventory at economic quantities, and maximizes plant output by preventing spillage, system clogging and process upsets. In chemical process industries (CPI) applications, level measurement of liquids, powders and slurries are often complicated by the presence of steam, dust, foam, turbulence, caking or condensate, as well as high temperatures and pressures.
The diversity of challenging conditions dictates multiple technologies for level measurement, which can be divided into point level measurement and continuous-measurement techniques. Point-level measurement monitors material level at a predetermined point, which could be a high level to avoid spillage, or a low level to avoid running empty. Continuous level measurement monitors materials constantly, noting any fluctuations and changes. Here, brief descriptions of common level--measurement technologies are presented.
Mechanical floats
A low-density float is attached to a horizontal rod that is mounted to a tank wall and linked to a switch. As the level rises and falls, the switch opens and closes. Mechanical floats are inexpensive, easy to install and work well for a variety of fluid densities. However, the float is calibrated to the density of the liquid it measures, so if the density changes, the float must be recalibrated. Another limiting factor for mechanical floats is buildup of material on the float.Differential pressure
The high-pressure side of a differential-pressure instrument is connected to the bottom of the tank, while the low-pressure side is connected to the vapor space in the top of the tank. The measuredpressure differential is the pressure of the liquid column of the tank. Changes in the liquid composition or temperature can create a false reading, but if the fluid density remains constant, this technique provides a true level reading. Differential-pressure devices require sealed fluid in pressurized vessels.

Electromechanical devices (Figure 1)
Capacitance (Figure 2)
A capacitor stores electrical energy and is made up of two parallel conductive plates separated by an insulator (dielectric material). The capacitor consists of a metal probe that typically contacts the material in a vessel. The metal probe senses the amount of material by measuring the differencein the probe’s capacitance when either air or material is present. The measurement system also requires an earth reference to complete any circuit and allow current flow. Capacitance technology is widely used, can handle a range of applications, and produces accurate and repeatable results. Chemical compatibility with the device must be taken into account,
since capacitance is a contact technique. Any changes due to temperature or chemical composition cause the dielectric property of the material to change, resulting in errors and the need to recalibrate. With one opening required in a vessel, capacitance technology is easy to install, and has no moving parts to wear out. Custom probes are available for aggressive chemicals. Calibration of capacitance instruments is best done manually, which can be time-consuming.
Ultrasonic (Figure 3)
Ultrasonic technology uses a piezoelectric crystal stored inside a transducer to convert an electrical signal into sound energy. The sound energy is fired toward the material, and reflected back to the transducer, which then acts as a receiving device, converting the sound energy back into an electrical signal. A signal processor analyzes the return echo and calculates the distance between the transducer and the target. The time lapsebetween sound burst and return echo is proportional to the distance from the transducer to the material in a vessel. Ultrasonic technology is a preferred option for continuous level measurement. Since ultrasonic instruments measure from
top down, there is virtually no contact with the material. Ultrasonic technology is easy to install and has no moving parts. In addition, it is not affected by changing dielectric properties or vessel shape. However, dust, vapor or foam can affect even the most advanced devices.
Radar (Figure 4)
Radar devices transmit an electromagnetic wave toward a material, where it is reflected back to the source. The total transit time to and from the target is calculated and is directly related to the distance. Pulse radar is similar to ultrasonic, in that fixed frequency pulses are transmitted to a material and reflected back to the source, and the time of flight is measured. Frequency-modulated, continuous-wave radar devices continuously transmit a range of frequencies, and a receiver monitors them. The difference between the transmitter and receiver frequency is directly proportional to the distance to the target. Since radar uses an electromagnetic wave, it does not require a carrier medium, and therefore is unaffected by environmental factors, such as temperature, turbulence, humidity, pressure, vapor, dust and others. Radar is noncontacting, and easily installed without disrupting a process.Magnetostrictive
Magnetostrictive level sensors measure the distance between a float magnet and the electronics-head end of the sensing rod. The float magnet is a permanent magnet, often in the shape of a ring, that travels along the sensing rod. The rod is mounted along the vertical axis of the vessel, and the head has an electronics module that transmits the float’s position information to a controller. Magnetostrictive systems, which rely on magnetomechanical properties of ferromagnetic materials, such as iron, nickel and cobalt, are highly accurate and are not affected by vapor, foam, dust or dielectric variations.Hydrostatic pressure sensor
This type of sensor measures level of a liquid in a tank by measuring the pressure exerted by the weight of the liquid. Hydrostatic pressure sensors are either externally mounted, where the measurement is based on the distance from the bottom of the tank, the pressure exerted by the liquid and the reference pressure, or submersible, which are used for open-air applications. ■So summing up all this:
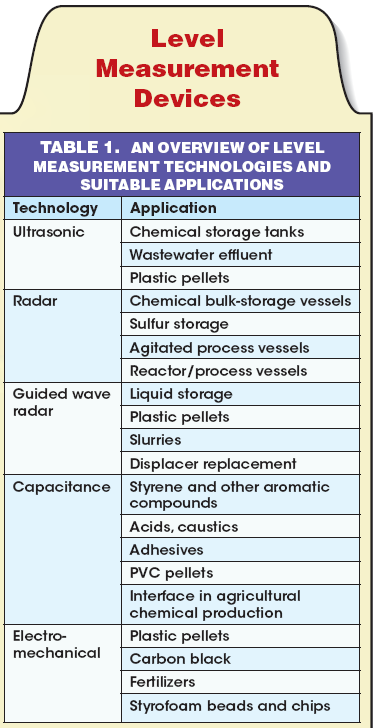
ioncube-
Country :
Posts : 45
Likes Total : 7
Join date : 2012-02-02
Location : Lahore/Faisalabad
Page 1 of 1
Permissions in this forum:
You cannot reply to topics in this forum